The Indian steel industry, a critical component contributing to around 2% of the country’s Gross Domestic Product (GDP), faces a transformative challenge in reducing its CO2 emissions and carbon footprint through the adoption of green steel production method. With global markets increasingly demanding environmentally sustainable products, India’s push towards green steel is crucial for meeting EU emissions norms and securing a competitive edge in the energy transition era.
As India takes initial steps towards this goal, the journey involves overcoming obstacles such as high production costs and infrastructure development for green hydrogen, which is key to lowering the carbon footprint of steel production. This transition not only aims to combat climate change but also aligns with global demand trends and government initiatives to position India to thrive in the shifting landscape of global steel production
Understanding the EU's Carbon Border Adjustment Mechanism (CBAM)
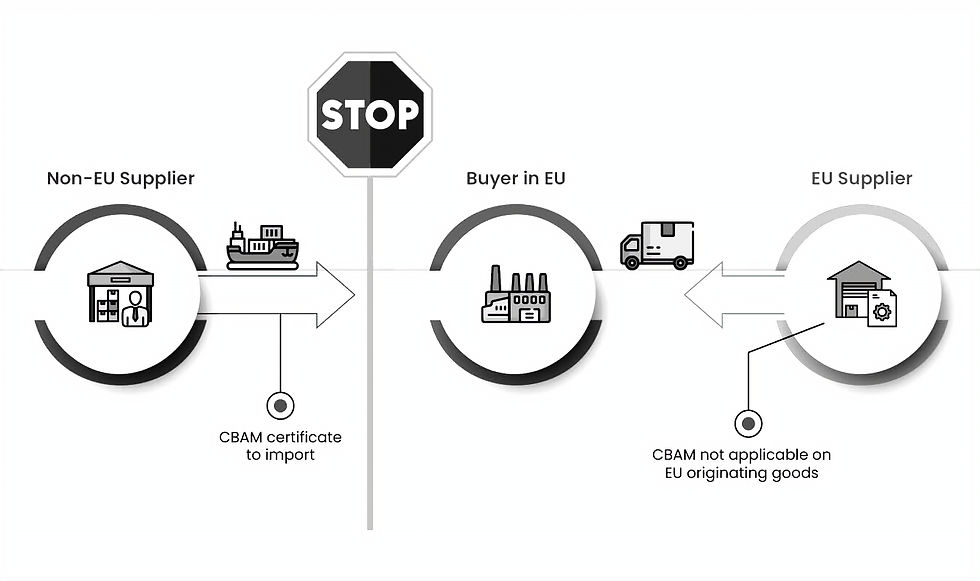
The European Union's Carbon Border Adjustment Mechanism (CBAM) stands as a pivotal development in the global steel industry, particularly affecting Indian steel exporters. Here's a breakdown of its key components:
Objective and Implementation: The CBAM aims to level the playing field between EU producers and international exporters by imposing a carbon price on imports of carbon-intensive goods, including steel. This mechanism is designed to encourage cleaner industrial production worldwide. Initially, from 1 October 2023, importers of specific products such as iron and steel will need to report the carbon intensity of these products quarterly to the CBAM Authority. The mechanism is set to fully apply in its definitive regime from 2026, expanding its coverage to more sectors and introducing a certificate trading system for importers based on the emissions embedded in their imports.
Global Partnerships and Impact: The CBAM is part of broader efforts, including negotiations for a Global Arrangement on Sustainable Steel and Aluminum (GASSA) with the United States. These initiatives aim to increase trade in "green" steel and aluminum, addressing the high carbon content of these industries which account for nearly a third of global industrial emissions. The CBAM and GASSA together signify a shift towards linking market access to carbon intensity, potentially reshaping global supply chains towards sustainability and supporting industrial decarbonization.
Challenges and Responses: Indian steel producers may face challenges due to the CBAM, as it could impose additional costs on exports to the EU, especially for those using more polluting processes. This mechanism also seeks to prevent 'carbon leakage,'where production moves to countries with less stringent emissions regulations. To comply with and benefit from these changes, Indian steelmakers are encouraged to adopt cleaner production methods, reducing their carbon footprint to meet the CBAM requirements and capitalize on the growing global demand for green steel9.
The Carbon Footprint of Indian Steel Production
India's steel industry, a significant contributor to the nation's GDP, is also a major emitter of carbon dioxide (CO2), accounting for about 12% of India's total emissions. The emission intensity in the Indian steel sector is notably higher than the global average, with 2.55 tonnes of CO2 emitted per tonne of crude steel produced, compared to the global average of 1.85 tonnes.
This high carbon footprint places Indian steel producers at a disadvantage, especially as global markets, including the European Union, increasingly demand lower carbon materials. The situation is further exacerbated by the fact that India emits 2.6 tonnes of carbon per tonne of steel, which is significantly higher than the global average. This discrepancy could lead to potential duties on Indian steel exports, impacting the competitiveness of Indian steel in key markets.
In the fiscal year 2023, India's steel production saw an increase, with the production of finished steel reaching 123 million tonnes, marking a 7.6% increase over the previous year. However, the steel industry's carbon footprint remains a pressing issue. Annually, the steel industry is responsible for around 240 million tonnes of CO2 emissions, a figure expected to double by 2030, driven by the Indian government's infrastructure development targets. This rapid increase in emissions underscores the urgent need for the adoption of cleaner production methods, such as green hydrogen-based steelmaking, despite its higher costs.
The Indian steel industry's structure further complicates the transition to greener technologies. The industry comprises two types of facilities: smaller local direct reduced iron (DRI) facilities and larger blast furnace-basic oxygen furnace (BF-BOF) facilities.
The larger steel producers, which account for 63% of total production, cater to an international market and are more likely to seek funding for greener technologies. This dichotomy within the industry highlights the varied challenges and opportunities for reducing the carbon footprint of Indian steel production.
Adopting CCUS: Strategies and Challenges for Indian Steel Makers
Adopting Carbon Capture, Utilization, and Storage (CCUS) presents both opportunities and challenges for Indian steel makers. Implementing CCUS technologies can help mitigate the industry's carbon footprint, aligning with global sustainability goals.
However, the high capital costs and technological complexities associated with CCUS adoption pose significant challenges for Indian steel manufacturers. Overcoming these hurdles will require strategic partnerships, government support, and focused research and development efforts to make CCUS a viable and sustainable solution for the Indian steel industry.
Collaboration and Future Directions:
Industry and Policy Maker Collaboration: Enhancing cooperation between Indian steel producers and EU policymakers can facilitate smoother transition and compliance with EU norms.
Sector-wide Cooperation: Achieving net-zero emissions by 2070 requires an incentive-based approach for all steel facilities, leveraging existing policy tools and focusing on technological upgrades and cleaner fuel use.
By addressing these challenges and leveraging government support, Indian steelmakers can pave the way for a sustainable and competitive future in the global steel market.
Through the exploration of initiatives such as the adoption of green steel, carbon border adjustment mechanisms, and strategies to reduce the carbon footprint, it's clear that the Indian steel industry stands at a pivotal crossroads. Addressing these challenges head-on, by embracing technologies like green hydrogen and Carbon Capture, Utilization, and Storage (CCUS), not only aligns with global decarbonization goals but also ensures India's competitiveness in a greener future.
The journey towards sustainability, while fraught with hurdles like high production costs and the need for robust infrastructure, is paramount to meeting EU emissions norms and driving the global demand for environmentally sustainable products.
FAQs
The "Green Steel for Europe" initiative is aimed at guiding the EU towards its 2030 climate and energy goals, as well as its 2050 strategy for achieving a climate-neutral continent. This involves implementing effective, clean steelmaking solutions.
The Indian steel industry can enhance energy efficiency and reduce greenhouse gas emissions by adopting Best Available Technologies (BAT). Notable methods include: a) Generating power from the waste heat of Coke Dry Quenching (CDQ). b) Recovering heat from sinter plants for power generation.
To decarbonize, the Indian steel sector must focus on Carbon Capture and Utilisation/Storage (CCUS) systems, which are expected to account for 56% of emission reductions. Significant investments in developing a CCUS ecosystem are essential for this transformation.
What Constitutes a Green Method of Steel Production? Green steel production can be realized through several strategies, including: a) Minimizing the use of carbon-based reducing agents and fuels in pelletizing. b) Transitioning from traditional blast furnace processes to electric arc furnaces that use steel scrap and direct reduced iron, powered by renewable energy sources. c) Shifting from fossil-based fuels to hydrogen as a cleaner alternative.
Comments